 |
|
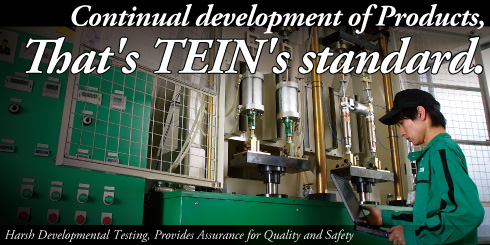 |
 |
Extraordinary 10 million strokes |
All 4 shock absorbers move constantly during driving. To test the product life, our shock absorbers are stroked repeatedly, over 10 million times each. That is equivalent to the load of about 5 years of use. Durability testing is being done around the clock and the shock absorber stays on the testing equipment for about 60 days.
Speed of the piston on the tester is 0.6m/s, simulating the most violent movement of shock absorber on street. The temperature inside the shock absorber reaches 80 to 100°C, which is hotter than the conditions the shocks would experience on a Super Taikyu race car in mid-summer. Testing imposed on TEIN products is unbelievably tough and precise. Durability is not the only thing tested, but all parts are disassembled and inspected for abnormality. These tests are performed on all TEIN products, not just race-use products.
TEIN strives to improve performance and durability of products, fully utilizing the most-advanced testing equipment. Severe tests are done daily for superior quality. TEIN does whatever it takes to provide all customers with safety and peace of mind. |
 |
All kinds of road conditions re-enacted |
Hydraulic Damper Tester precisely re-creates various road conditions and obtains data. This could be a lap around the Nurburgring circuit, or it could be a trip around the TEIN office on public roads. With this tester, movements of the shock absorber are truly reproduced, allowing TEIN to measure inner pressure and/or other details instantly. This reduces the need for testing with real vehicles, thus drastically cutting down the time required for testing. Time required for product evaluation is much shorter than before, as engineers can more quickly test initial damping force settings for each vehicle application.
Hybraulic Shaking Tester→ |
 |
Rustless; proof of TEIN technology |
Sooner or later, iron rusts. But with outstanding surface treatment, occurrence of rust can be minimized. TEIN uses a "Salt Spray Tester," to test the corrosion resistance of various surface treatment methods.
Salt water is sprayed in testing chamber for 96 hours continuously, which is equivalent to about 1 year of regular use. Competitors' products are also tested for comparison. This testing led to the development of our exclusive painting technology that can withstand conditions from heavy snowfall areas. |
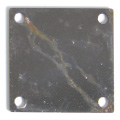 |
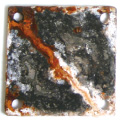 |
Surface treatment used
on TEIN products |
Surface treatment widely used
on competitors' products |
|
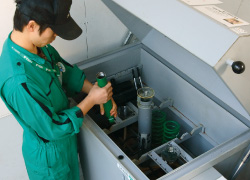 |
|
 |
Bring out the full potential of every single part |
TEIN has introduced the latest CAD / CAE systems, which let computers assist design and analysis. Strength analysis of each and every part can be simulated on computers. This combined with real strength testing brings out the full potential of even the tiniest parts.
Also, custom-developed programs ensure better product designs and analysis, to reduce development time and costs. |
|
01 02-(1) 02-(2) 03 04 05 06 07 08 09-(1) 09-(2)  |
|
 |